Mechanical Behavior of Polymer Blends
Many polymer products consist of blends of polymers, and in some cases, they consist of block or graft polymers. The polymers or polymer blocks are usually phase separated. Frequently, one of the phases is elastomeric and the other is plastic or glassy. The mechanical behavior of such a system can be quite complicated. To describe its creep and stress relaxation behavior, the system may be replaced with an array of rubbery (R) and glassy (G) phases, as depicted below.
The viscoelastic response in creep and relaxation experiments of such a model system can be easily analyzed if we assume simple elastic behavior of each phase, that is, Hooke's law, σ = E · ε, applies to both the elastic and glassy phase.
For the parallel or isostrain model (left side Figure), the two bars have to remain parallel and horizontal throughout the experiment, which means that the strain is equal in both bars (εR = εG). Then
σ = σR + σG
σi = εi Ei; i = G, R
E = (1- λ) EG + λ ER
This represents the upper bound to the achievable modulus of a polymer system consisting of a rubbery and glassy phase.
If the two bars are connected in series (right side Figure), both elements are subjected to the same stress (σR = σG), whereas the strain is additive:
εtot = εG + εR
yielding a Young's modulus of
E = (φ / ER + (1 - φ) / EG)-1
The isostress model represents the lower bound of the modulus of a polymer system consisting of a rubbery and glassy phase.
Indeed, it is possible to create polymer blends of glassy and rubbery polymers that show a mechanical behavior that is very close to these two limiting cases, that is, the two equations for the Young modulus are a good approximation for those of real polymer blends.
Elastic Modulus of Two-Phase
System
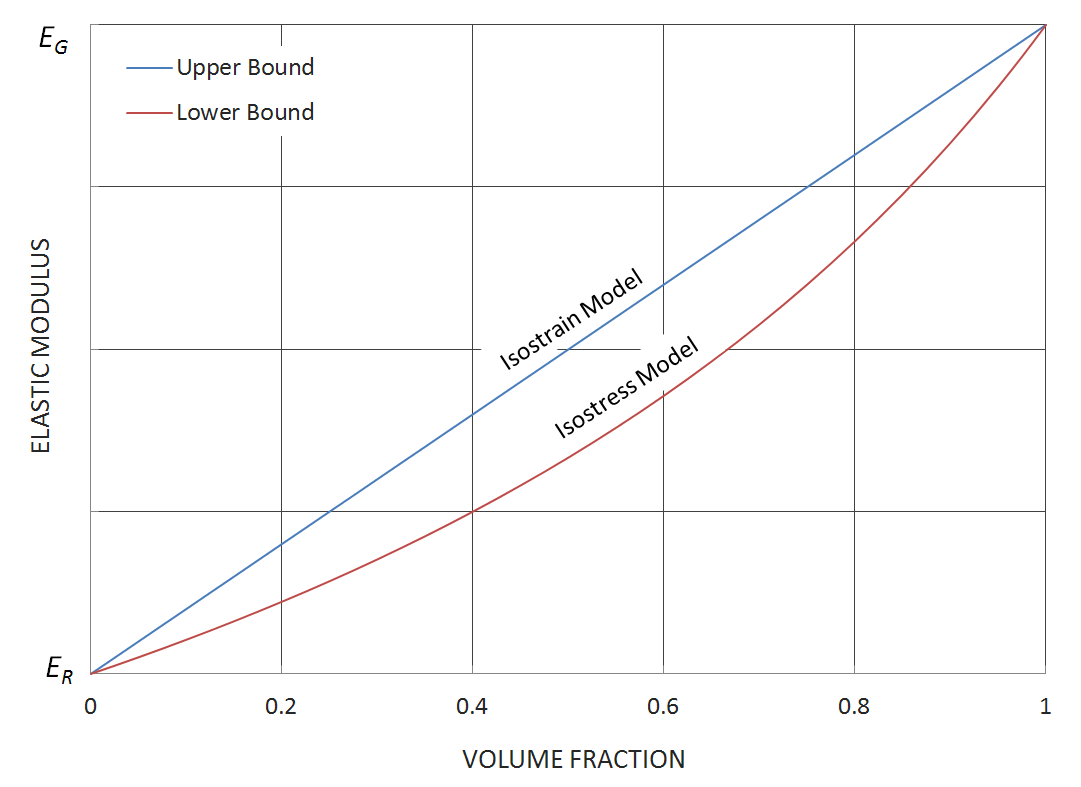
Elastic Modulus of Two-Phase System
In general, the mechanical behavior of a polymer blend will depend on the phase morphology. For example, when the rubbery phase is continuous in space and the glassy polymer is dispersed, the material is soft and the lower bound is a good approximation. If, on the other hand, the glassy phase is continuous and the rubber phase is dispersed (discontinuous), the material is rather stiff and the upper bound is a good approximation for the real behavior of the blend.
While these simple models are a good representation of the behavior of some polymer blends, more complicated arrangements of arrays of rubbery and glassy phases have to be created to describe the behavior of systems with a more intricate morphology. Two examples, of such systems are shown below.
The Young's modulus of these systems are given by
E = λ [φ / ER + (1 - φ) / EG] + (1 - λ) EG
E = [φ / [λ ER + (1 - λ) EG] + (1 - φ) / EG]-1
The models above can also be applied to composite materials. For example, a composite of continuous glass fibers in a polymer matrix can be described with the parallel array of phases if deformed in the direction of the fibers.