Hardness of Plastics and Rubbers
Hardness is defined as a material’s resistance to permanent indentation. It is one of the most measured parameters and often reported on technical data sheets of plastics and rubbers.
Hardness of ductile materials is essentially a measure of their plastic properties. In the case of yield and tensile strength, a more or less linear correlation between hardness and mechanical strength is often observed (see Figure below). However, the hardness of a material is not always a good predictor of other properties such as strength, resistance to scratching, abrasion or wear, and therefore, should not be used alone for product design. For example, at low hardness or low strength levels, it is expected that the two quantities have a nonlinear correlation.
Relationship between Strength and Hardness
of Amorphous Polymers
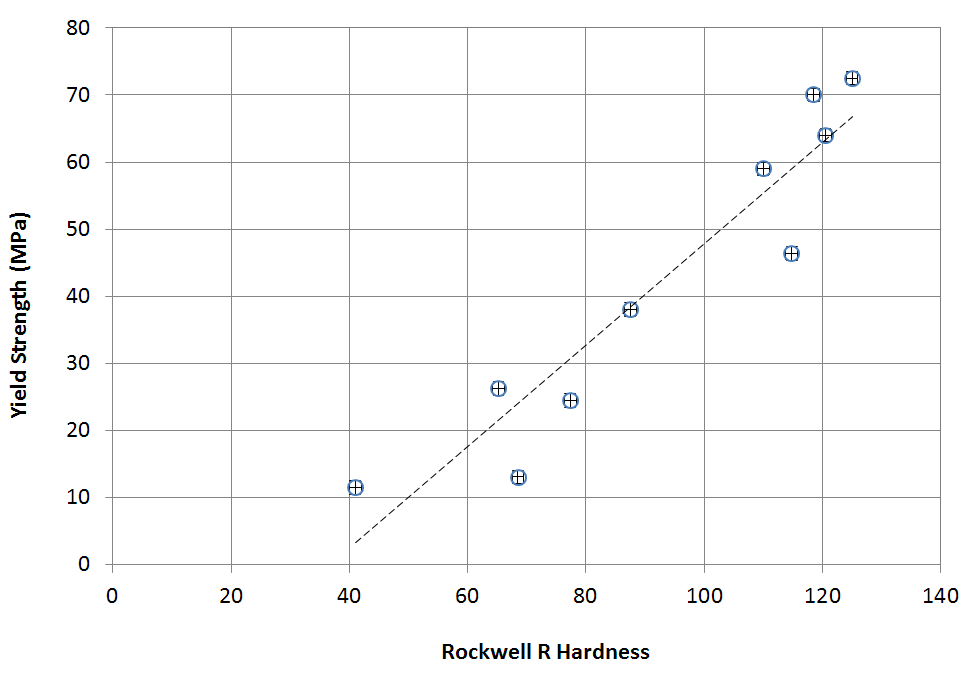
Relationship between Strength and Hardness
of Amorphous Polymers
The hardness of plastics and rubbers is often measured by the Rockwell or Shore (durometer) hardness methods. Both methods provide an empirical hardness value, which do not necessarily correlate with other physical properties. The Rockwell hardness is usually chosen for "harder" materials such as steel, polycarbonate, polystyrene, polymethacrylates and acetal where the creep of the polymer has a lesser effect on the result, whereas the Shore durometer is often preferred for softer materials, such as soft polymers, elastomers, and rubbers.
In the case of Rockwell hardness, a specimen of at least 1/4 inch (6.35 mm) thickness is indented by a hard steel ball. First, a small preload is applied, and the apparatus is zeroed, then a larger load is applied and removed. After a short time with the preload still applied, the remaining indentation is read from the scale.
In the case of Shore hardness, a spring-loaded needle is placed against the rubber or plastic and pressure is applied. After the needle has penetrated as far as it can go, the depth of indentation of the needle is measured which is proportional to the hardness of the plastic/rubber.
The depth of indentation not only depends on the hardness of the material but also on its viscoelastic properties, the shape of the indenter, and the duration of the test.
There are several Shore hardness scales for measuring the hardness of different materials. The most frequently used scales are Shore A and Shore D. The Shore A scale measures rubbers and gels that are very soft. Some semi-rigid plastics can also be measured on the high end of the Shore A scale. The shore D hardness scale measures the hardness of hard rubbers, semi-rigid plastics and hard plastics.
The Rockwell hardness scales use different size steel balls and different loads. The three most common scales used for plastics are Rockwell E, M, and R; other Rockwell hardness scales are used for metals, with Rockwell A, B, and C being the three most common scales. The correlation between the different Rockwell scales used for plastics is rather poor and, therefore, conversion between the scales is discouraged, that is, both the geometry of the indentor and the applied force influence the measurements.